In the intricate world of machinery, where metal meets metal and gears dance in harmony, a silent hero plays a crucial role in ensuring smooth operations – grease. Often overlooked, grease is a lubricant that keeps the wheels of industry turning, literally.
From the smallest bearings to the largest gears, grease is the unsung champion that prevents friction and wear, ensuring the longevity and efficiency of various machine parts.
Composition and Properties of grease
Grease consists of a semi-solid lubricating substance that combines a base oil, thickening agent, and diverse additives. The base oil can be vegetable oil, mineral oil, synthetic oil, or a combination of both, while the thickener is typically a metal soap.
The choice of base oil and thickener, along with additives, determines the grease’s performance characteristics, such as temperature resistance, load-bearing capacity, and water resistance.
Lubrication Mechanism
The primary purpose of grease is to reduce friction and wear between moving parts. When applied to machinery, it forms a protective layer that separates surfaces, preventing direct metal-to-metal contact.
This cushioning effect is crucial in high-stress areas where sliding, rolling, or oscillating movements occur. The thick consistency of grease allows it to adhere to surfaces and remain in place, even in vertical or overhead applications.
Common Applications of Grease
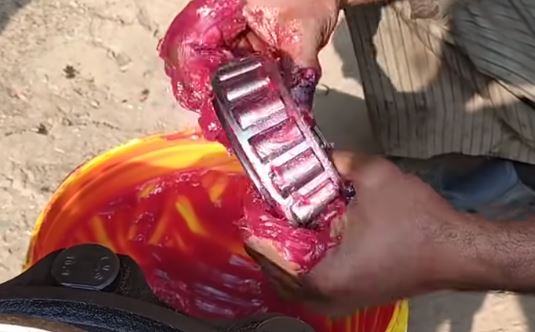
Bearings:
Bearings are one of the most common applications for grease. Whether in electric motors, industrial machinery, or automotive components, bearings rely on grease to ensure smooth rotation and prevent premature failure.
Different types of bearings, such as ball bearings, roller bearings, and plain bearings, may require specific grease formulations tailored to their operating conditions.
Gears:
Gears, the cogs that transfer power within machinery, operate under heavy loads and varying speeds. Grease provides essential lubrication to reduce friction between gear teeth, preventing excessive wear and extending the life of the gears.
Chains:
In chain-driven systems, such as those found in motorcycles, bicycles, and industrial conveyors, grease is applied to the chain links to minimize wear and reduce the noise generated during operation.
Joints and Bushings:
Grease is commonly used in various joints and bushings, such as those in suspension systems, steering components, and articulating machinery. It ensures smooth movement and minimizes the impact of vibration and shock.
Benefits of Using Grease
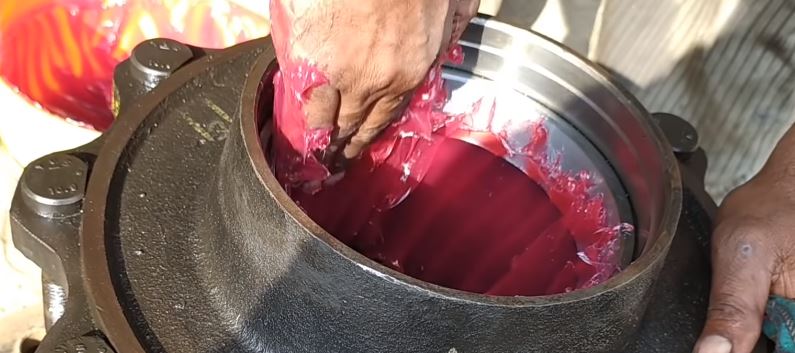
Extended Component Life:
Properly lubricated components experience less wear and friction, leading to an extended service life. Regular greasing of machine parts helps prevent premature failure and costly repairs.
Reduced Friction and Heat:
Grease creates a protective barrier that reduces friction and heat generation during operation. This is particularly important in high-speed or heavy-load applications where heat can lead to component failure.
Water Resistance:
Greases with water-resistant properties are vital in applications exposed to moisture or humidity. Water-resistant greases prevent corrosion and maintain their lubricating properties even in challenging environments.
Sealing Properties:
Grease’s thick consistency allows it to seal out contaminants, such as dust and dirt, protecting sensitive components from abrasive particles that could compromise performance.
Conclusion
In the intricate dance of gears, the smooth rotation of bearings, and the rhythmic movement of chains, grease stands as a silent guardian, ensuring the seamless operation of machinery. While often taken for granted, the proper selection and application of grease play a pivotal role in preventing wear, reducing friction, and extending the life of critical machine components. As industries continue to advance, the unsung hero, grease, remains an indispensable ally in the pursuit of efficient and reliable machinery.
1 thought on “Grease and Its Crucial Role in Machinery Lubrication”
Comments are closed.